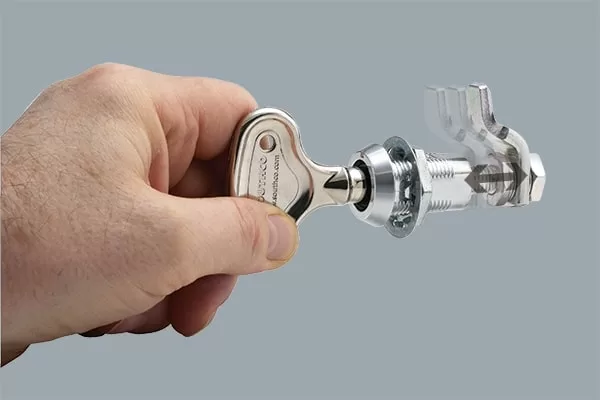
The general population encounters latches every day. From the magnetic handle that opens a kitchen cabinet door to the latch that releases a car hatchback door, latches are used everywhere. Simply put, a latch is a fastening device that joins two surfaces together, while still allowing or restricting access to the enclosure’s interior.
Cam latches are a simple, cost effective latch type that engineers can utilize in their application. This type of latch consists of a body that is typically attached to a moving panel or door, and incorporates a cam lever that can be rotated to engage a non-moving or fixed panel. Once the door is closed, the cam rotates behind the fixed panel to secure the moving panel or door.
Compression Latch
A compression latch is almost identical in functionality to a cam latch in that it is composed of a body and cam lever that can be rotated when actuated by hand or tool. However, with a compression latch, the cam creates a clamping force between the two surfaces.
A push-to-close latch holds doors or panels securely by simply pushing the door closed. This type of latch is also known as a “slam latch”, due to its innate ability to resist any damage when a door or panel is slammed shut. Unlike some other latches, the handle does not need to be turned in order for the latch to engage.
The way that a slam latch functions is straightforward. The latch, attached to a swinging door or panel, consists of a body and a cam that is spring loaded. When the panel or door is closed, the cam is either pushed in against a mating surface or hooks around a striker. The cam will then either spring back out behind the mating surface or lock around the striker to secure the panel or door in place.
Draw latches utilize tension to pull two surfaces securely together in the same plane. This type of latch is typically made up of two pieces. The first piece will be attached to one panel and acts as an operating mechanism. The second panel will have the securing mechanism mounted, which acts as a keeper. Tension is created when the lever is hooked to the keeper. Draw latches can reduce vibration or rattling and also provide compression. Due to its simplicity, the draw latch is typically externally mounted on engine hoods to HVAC equipment. Engineers that are designing a simple application may find that a draw latch offers the most cost-effective solution.
Sliding Latch
A sliding latch is made up of a sliding or rotating body attached to one surface, while the stationary keeper will be attached to the other surface. The two surfaces will become secure when the sliding or rotating piece moves behind the stable piece. Slide latches can be designed to resist both vibration and rattling. Actuation will typically be performed manually. There are multiple styles and materials available for sliding latches, depending on the end application and load requirements. Choosing the appropriate latch type for any given application requires the engineer to gather all of the relevant information that could affect latch performance, including size, force, weight and environmental factors, such as whether the latch will be used indoors or outdoors.
Indoor Latches
Generally, indoor applications do not have as strict requirements as outdoor applications. Engineers will not have to worry about outside environmental factors, such as UV rays and rain, as indoor latches will not need to withstand the elements. Engineers can choose latches constructed of economic materials such as plastic or zinc in order to keep overall costs down. The level of security needed for indoor applications may also be lower compared to outdoor applications. Non-locking latches could be appropriate depending on access control needs within interior environment.
Outdoor latches have much stricter requirements compared to indoor latches. Engineers will have to account for all environmental factors and weather events, from ice to high humidity. This can lead to design considerations including corrosion resistance and material degradation.
Mechanical or Magnetic Latching
Another consideration that engineers need to take into account is the latching method. Certain types of latches provide mechanical or magnetic latching to secure the door, cabinet or panel. Some latches have electronic capabilities where the user does not need to apply any direct actuation to secure the latch.
Visible or Hidden Latches
Choosing a hidden or visible latch will depend on the end user’s requirements and operating environment. Visible latches are used when the user needs to see the latch in order to actuate it. Latches may need to be concealed for security reasons, in which case they can be installed behind a door or panel, out of sight. Hidden latches also allow for clean, uninterrupted surfaces, which can improve the appearance of a product or piece of equipment, such as a refrigerator door or gaming machine.
Custom Latches
Engineers should consider working with an experienced supplier to ensure that they are choosing the right type of latch for their application. The chosen latch should perform as intended to allow or deny users access to an enclosure. Selecting the appropriate latch type is not only important for proper application performance, but can also impact user perception. For example, a car owner will appreciate the satisfying feel of closing a glovebox if a high quality latching solution has been chosen. This can also improve their overall perception of the vehicle’s quality.