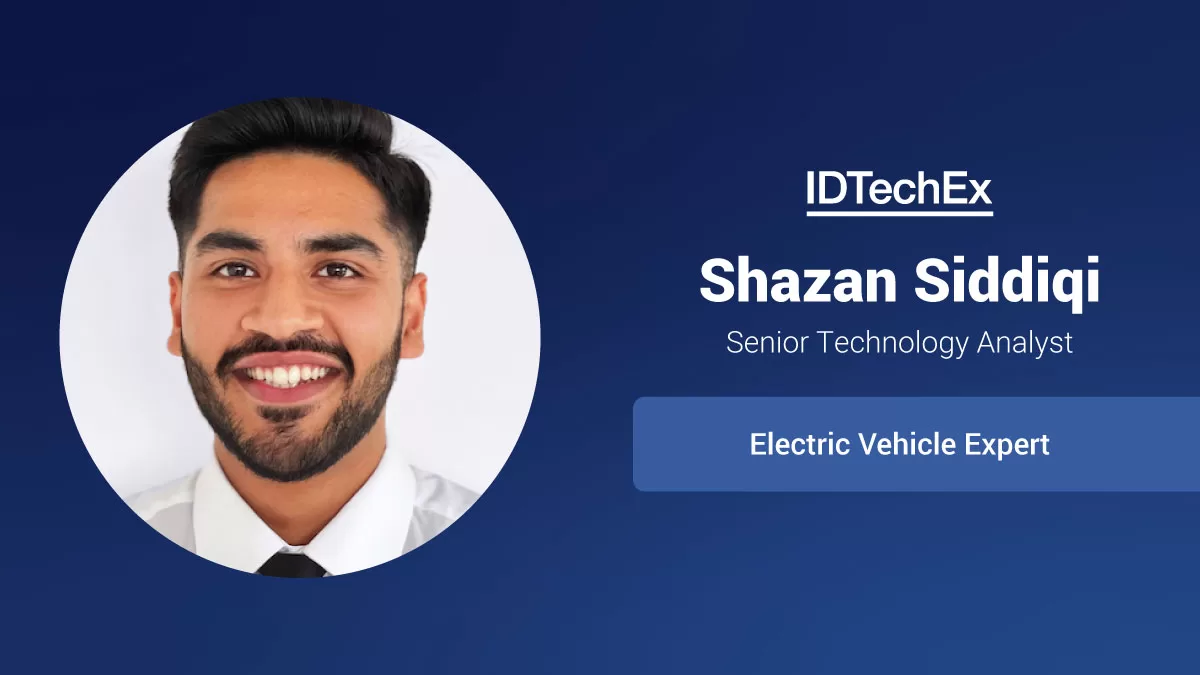
Author: Shazan Siddiqi, Senior Technology Analyst at IDTechEx Many people were surprised when HiNa revealed their lineup of sodium-ion battery cells, as well as a prototype of an electric car, in February 2023. But it had been a long time coming. The low-cost Sehol E10X microcar uses a 25 kWh battery pack made from cylindrical sodium-ion cells from HiNa. The business commissioned its first 1 GWh/year production line in December 2022. The complex will host five such lines; another for 30 GWh/year is planned, and more batteries will be manufactured under license. Plenty of competition, like CATL, Svolt, Farasis, Lifun, DFD, Transimage, and others are currently working on their own sodium-ion batteries to be mass-produced this year. Market analysis by IDTechEx in November 2023 suggests an anticipated growth of approximately 40 GWh of SIBs alone by 2030 at a minimum, but up to an additional 100 GWh of manufacturing capacity is projected if the market is successful by 2025. The scene is set for another upset in the battery industry in the coming years, similar to the large-scale emergence of LFP in 2020. IDTechEx anticipates that sodium-ion batteries will first penetrate the A00 vehicle segment (small, low-speed EVs) in China as they are mostly used as urban commuters and do not require an extended range. The energy density of A00 class vehicles in production is mainly concentrated between 140 and 160 Wh/kg (pack level), and the cruising range is typically under 250 km, according to IDTechEx research. Current sodium-ion batteries can largely meet these requirements, as shown in the IDTechEx report “Sodium-ion Batteries 2024-2034: Technology, Players, Markets, and Forecasts”, which benchmarks cells from various players in the market. Very recently, a race has emerged in China to be the first to use sodium-ion cells in high-volume electric microcars, with Farasis, HiNa, and CATL announcing plans to supply sodium-ion cells to JMEV, Sehol, and Chery for use in their A00 class models respectively. A00 electric vehicle manufacturers are highly sensitive to costs, and the application of sodium-ion batteries has certain advantages. In the long run, when sodium-ion batteries can be manufactured at scale, they are expected to have a 20-30% price advantage over Li-ion batteries.
|
||
Sodium-ion batteries have characteristics comparable to lithium iron phosphate (LFP), suggesting that low-speed, micro EV applications are possible. Source: IDTechEx |
||
While LFP batteries have improved since 2015, what has improved even more is the engineering of battery packs. The Sehol E10X’s battery pack is air-cooled, using racks of cylindrical cells, retaining an energy density of 120 Wh/kg on the pack level. In terms of weight, this is 96% of the 125 Wh/kg energy density of the 54 kWh LFP pack in the standard range Tesla Model 3 first announced in 2020. But in terms of volume, this air-cooled pack would not be competitive. Nor do the prismatic cells from HiNa with their volumetric energy density of 263-283 Wh/L seem to be a useful replacement for LFP cells with 380-450 Wh/L at first glance. However, the engineering of cell-to-pack (CTP) battery packs has improved immensely even in the few years since they were first talked about in 2019. CATL announced their sodium-ion batteries in 2021 alongside a prospected integration efficiency of over 80%. Such packs make even first-generation sodium-ion batteries viable as a direct replacement for older generations of cars with LFP battery packs of the early 2020s. Even based on performance, the sodium-based battery would be preferable to cars with older LFP packs. They can fast charge from 10% to 80% within 15 to 20 minutes and only lose 10% of capacity at -20°C. Sodium-ion batteries can also be fully discharged without the risk of catastrophic battery failure upon recharge, as would be the case in lithium-ion batteries due to copper current collectors in the anode. CATL expects to sell their batteries with Prussian blue cathodes for as little as US$30/kWh to US$45/kWh in mass production due to the lower material cost of iron-based cathode and synthesis without the need for high-temperature calcination. Cells with more advanced layered oxide cathodes are widely expected to reach 200-220 Wh/kg and between 400-500 Wh/l in the next few years before the end of the decade. This will enable EVs to reach over 500 km range without the use of lithium. This will fundamentally change the battery market. However, the energy density of high nickel NMC cathodes is 20-40% higher than any known sodium-based cathodes that might be commercialized. But this will not make sodium-ion batteries redundant. Cost matters more than energy density. It is important to remember that to this day, there is a 400 GWh/year industry for lead-acid batteries despite their low energy density of just 35 Wh/kg. Sodium-ion batteries, based only on abundant materials like sodium, iron, manganese, carbon, aluminum, and the like, are sufficient for EVs with a practical range of around 300 km — even in their current primitive form. With no constraints on critical resources, this should help alleviate many geopolitical tensions currently building up around access to battery materials like lithium, nickel, cobalt, and graphite. The IDTechEx report “Sodium-ion Batteries 2024-2034: Technology, Players, Markets, and Forecasts” provides in-depth coverage of this emerging industry. To find out more about this IDTechEx report, including downloadable sample pages, please visit www.IDTechEx.com/Sodium. |